Le LEAN Construction
Des chantiers plus performants
Aborder autrement le chantier en chassant tous les gaspillages, du stockage des matériaux jusqu’à la réception de l’ouvrage : c’est l’objet du Lean Construction. Une méthode légère et collaborative qui amène tous les acteurs de l’entreprise à se poser la même question : comment travailler plus efficacement, individuellement et ensemble.
Principes du Lean construction
REX chantier Epinal Habitat
Action expérimentale
Des ressources
Grands principes du Lean construction
Origines du Lean Construction
Inspirée des méthodes de production de Toyota, telles que présentées par James Womack et Daniel Jones dans leur livre « Lean Thinking », le Lean Construction ou gestion de projet « LEAN » se traduit par le terme « sans gras ».
Bien que développé par le Lean Construction Institute 2 depuis le début des années 90, le Lean Construction est encore peu connu en France. Le Lean Construction transpose les cinq principes de la gestion de la production « au plus juste », tels que définis par Womack et Jones, jusqu’à la livraison des projets :
- Déterminer la valeur exacte de chaque produit conçu et/ou manufacturé.
- Définir la chaîne de valeur correspondant à chaque produit (chacune des étapes de production).
- Établir des flux de valeur continus (c’est -à-dire éliminer les étapes inutiles, sans valeur ajoutée ou créant des pertes de valeur).
- Laisser le client orienter la valeur. Viser la perfection.
Cette approche vise à maximiser la valeur, telle que perçue par le client final, à minimiser les gaspillages, et à diminuer les délais et les coûts.
Définition proposée
S’agissant avant tout d’un courant de pensée, chacun peut adapter la sémantique proposée à sa propre configuration.
Définition proposée par Patrick DUPIN, doctorant en Lean Construction à l’Université Trent de Nottingham (GB):
Philosophie visant à la création de valeur pour le Client par l’élimination des gaspillages soutenu par des outils collaboratifs de gestion de projets s’inscrivant dans le cadre d’une démarche systématique et rigoureuse d’amélioration continue.
Philosophie
Plus qu’un ensemble d’outils, le « Lean Construction » est avant tout une démarche intellectuelle portée au niveau universitaire par l’université de Berkeley en Californie (laboratoire PS2L) et par des entreprises telles que DPR et Turner aux USA développant cette démarche à l’ensemble de leurs opérations.
Création de valeur
Des recherches récentes (Glenn Ballard 2008) ont montré que seulement 15% à 30% des opérations sur chantier créent de la valeur pour le Client (ce pour quoi il paie).
Elimination de gaspillages
Le corolaire de la création de valeur est l’élimination des gaspillages. L’attente du séchage du béton d’une dalle (plancher) coulé en place est un exemple typique de gaspillage, donc de non création de valeur pour le Client. Le Client paie le fait d’utiliser une surface en béton et non l’action d’attendre qu’elle sèche, rendant toute opération sous celle-ci impossible à cause des forets d’étais.
Soutenu par des outils collaboratifs
Le Last Planner® System, outil phare de la démarche Lean construction force la collaboration entre les différents acteurs et parties prenantes du projet.
Démarche systématique et rigoureuse
Les résultats proviennent de la récurrence et de la rigueur avec laquelle la démarche est appliquée.
Amélioration continue
« Lean is a Journey, not a destination ». Ou en français « Le Lean est un voyage, pas une destination » : phrase emblématique du mouvement Lean illustrant le caractère infini de la démarche.
On peut tendre à la perfection, mais jamais l’atteindre.
Les gaspillages en gestion de projet
On peut maximiser les bénéfices d’un projet (sa valeur pour le client final et les autres parties prenantes) en minimisant les pertes associées aux méthodes traditionnelles de gestion de projet. Le tableau suivant (adapté des écrits récents de Greg Howell, Lauri Koskela et Hal Macomber, trois promoteurs importants de la gestion de construction ‘LEAN’, de Norman Bodek, un gourou de l’utilisation de la ‘Toyota Way’ ainsi que de mes propres écrits), fait le parallèle entre les pertes liées à la production d’un produit et celles liées à la gestion d’un projet.
Les 7 pertes en production
(gestion d’un flux matériel)
- Surproduction
- Attentes
- Transfert des matières
- Manutention superflue
- Inventaire déficient
- Mouvement excessifs (perte de flux)
- Produit défectueux
Les 10 pertes en gestion de projets
(gestion de flux matériel + humain)
- Attente d’intrants
- Transfert de l’information
- Informations superflues
- Comportements déficients
- Perte de bonnes idées
- +8 débrouille
- +9 résistance au changement
- et 10 non gestion des perceptions
Sources : Taiichi Ohno (gourou de la gestion de la production). 2004, Howell, Koskela, Macomber (gourous de la « Lean Construction ») 2007, Norman Bodek (« Toyota Way ») 2008, Claude Emond.
Les bénéfices d’un projet peuvent être optimisés en minimisant les pertes associées aux méthodes traditionnelles de gestion de projet.
Les gaspillages liés à la gestion d’un projet de construction proviennent de la nécessité de gérer à la fois un flux de matériel et de matériaux et un flux humain. Même si les mêmes principes « logistiques » peuvent s’appliquer d’un chantier à l’autre, il faut néanmoins les repenser à chaque chantier.
Deux principes de base et outils principaux
D’après une idée originale du Lean Construction Institute, développé par l’IGLC (International Group for Lean Construction), le Lean s’appuie sur deux principes :
- Un projet peut se gérer comme un « système de production », en contrôlant chacune de ses étapes pour en maximiser la valeur et en minimiser les pertes (Production Control).
- Un effort particulier doit être réservé à la conception, et à l’adaptation en cours de réalisation, de ce système de production temporaire « unique et différent » pour chaque projet, en collaboration avec toutes les parties prenantes (Work Structuring). La conception doit faire l’objet d’une attention particulière pour réduire les adaptations en cours de chantier et promouvoir la collaboration entre toutes les parties prenantes.
Dans ce contexte, la gestion de projet « LEAN CONSTRUCTION » se matérialise par des outils.
5S Chantiers
L’application de la méthode des 5S, outil complémentaire au lean construction, permet de construire un environnement de travail ad hoc : fonctionnel et régi par des règles simples, précises et efficaces. Il s’adapte en fonction des spécifiés propres des opérations de chacun.
Premier S = Seiri
Signifie en français « débarrasser ». Tout objet cassé, abimé ou inutile doit être mis à la poubelle. La plupart des gens gardent des choses qui n’ont aucune utilité et qui polluent l’espace commun.
Deuxième S = Seiton
Signifie en français « mettre en ordre ». Chaque chose doit avoir une place, chaque place doit avoir une chose. Le but est d’organiser un grand rangement utile. Définir les emplacements de chaque objet en créant un « rangement visuel » du même type que les outils d’un mécanicien où l’on peut voir le contour dessiné sur le tableau de rangement.
Troisième S = Seiso
Signifie en français « nettoyer ». Maintenant que la zone est libérée des ces encombrants et ordonnée, un bon ménage rendra le secteur plus propre. Il est d’autant plus facile à réaliser grâce aux deux étapes précédentes.
Quatrième S = Seiketsu
Signifie en français « maintenir propre ». Cette étape consiste à rendre durable ce chantier d’amélioration continue en s’obligeant à faire l’état des lieux de la zone régulièrement, avec les personnes utilisant cet espace afin d’y maintenir un ordre permanent.
Cinquième S = Shitsuke
Signifie en français « rigueur ». Cette étape a pour but de créer un audit par une personne étrangère à la zone afin de déterminer les améliorations supplémentaires à réaliser, toujours dans l’esprit d’augmenter ses performances.
Système du dernier planificateur (LPS)
C’est l’outil phare du Lean Construction !
Simple à utiliser basé sur Excel, notre outil est avant tout visuel et simple à utiliser sur chantier. Après une courte formation c’est l’ensemble des entreprises qui préparent leurs tableaux. Systématiser l’anticipation toutes les semaines, en définissant les tâches à réaliser dans une fenêtre glissante de deux semaines et en préparant les travaux à 2 mois (check list opérationnelle).
Equipes intégrées
IPT pour Integrated Project Teams : le client, les consultants, fournisseurs, entreprises, ouvriers ainsi que les utilisateurs constituent tous l’équipe de projet et fonctionnent en mode intégré.
Les conditions du projet et les changements sont passés en revue pour mieux les anticiper et tenir ses « promesses ». Les progrès du projet sont gérés à travers une série de « conversations » comparables au « scrum » en Agile Scheduling.
L’équipe doit penser à s’adapter collaborativement et collectivement plutôt qu’à optimiser son seul périmètre.
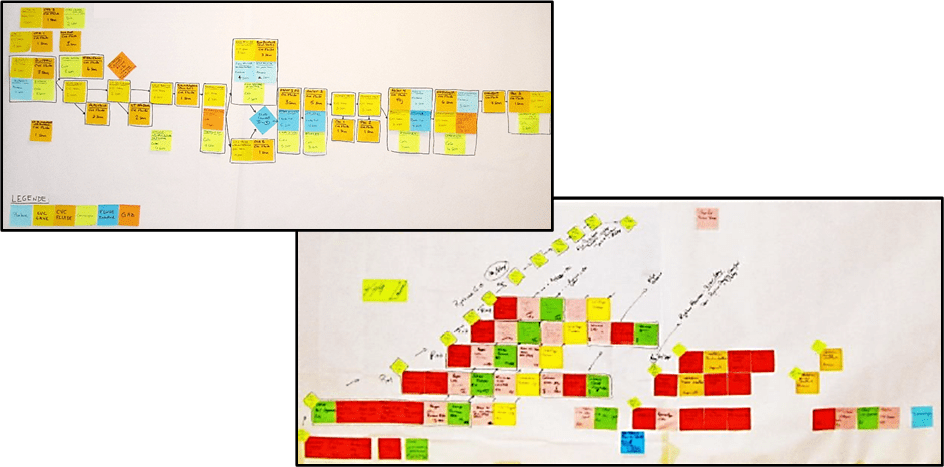
Le système de livraison de projet « LEAN »
Lean Project Delivery System™ (LPDS – marque déposée du Lean Construction Institute).
Un projet est processus de création de valeur.
L’aval (les entreprises et consultants spécialistes) doivent être impliqués dans la planification en amont (conception). C’est l’intégration multidisciplinaire (LPS et IPD).
Le contrôle de projet vise l’exécution à 100 % d’éléments concrets dans un temps donné (EVR) et l’évaluation ‘de ce qui reste à faire’, plutôt que de s’appuyer sur la détection de variations au plan après coup.
L’optimisation fiabilise les flux sur chantier et génère une augmentation de productivité.
Lean construction – retour d’expériences
REX Chantier Epinal Habitat
Projet Tambour Major
Rénovation de 180 logements occupés, répartis sur 6 Bâtiments :
- Mission OPC LEAN
- Suivi hebdomadaire du planning (LPS)
- Support pour avancement et contrôle des travaux
Objectifs du projet
1
Réaliser l’opération en 18 mois- MOA en charge cette partie
2
Faire travailler en séquences les entreprises et limiter les temps d’attente- Réalisation d’un planning collaboratif
- Déterminer les séquences avec les entreprises
- Identifier les impacts logistiques et les moyens communs
3
Faire collaborer les entreprises dans un but commun- Préparation des supports d’animation
- Accompagnement pour auto-contrôle
Séquences des tâches
Travail fait en collaboration avec la MOA, les partenaires économiques, la FFB et les entreprises en charge des lots.
Epinal Habitat réunion pour la réalisation des séquences
Exemple d’une des séquences vu avec les entreprises
Les séquences pour les travaux intérieurs
Exemple de planning CDF
Livrable
Mise en place de support pilotage contrôle
Exemple d’une des séquences vu avec les entreprises
Exemple de tableau pour le suivi des logements
Autocontrôles par étage de chaque logements, chaque pastille de couleur correspond à une entreprise
Planning collaboratif renseigné par les entreprises
LPS et supports en fonction du nombre de bâtiments en cours de réalisation.
Sur les photos on remarque un second tableau de planification et les plans pour auto-contrôle des autres bâtiments, de même les tableaux pour chaque bâtiment et les plans des façades. Le LEAN s’adapte en fonction des critères du Client.
Livrable
Vue de la toiture en cours de rénovation sur le TM03, couvertines partiellement posées
Fresque sur TM03 et échafaudage en place sur TM07
Echafaudages en place sur A116 et travaux façades sur TM05
Conclusions
Il est difficile d’émettre une conclusion globale et arrêtée sur cette expérience.
Les situations décrites ne correspondent pas forcément à tous les chantiers et à la réalité des entreprises.
Toutefois, il convient de bien anticiper la démarche dans les marchés avec une vraie implication de la démarche.
Toutefois, on peut apporter un éclairage sur quelques points précis nécessitant, dans le cadre d’une reproductibilité, une prise ne compte de ces difficultés.
Problématique RDV locataires
Malgré une bonne volonté évidente de la MOA, les rendez-vous sont pris mais les locataires ne sont pas toujours attentifs aux dates prises et sont absents du logement, bloquant de fait les travaux intérieurs. Pour optimiser cette prise de rendez-vous, une communication complémentaire pourrait être faite avec brochures et rappel par courrier. Eventuellement, il pourrait être proposé un logement « Tampon » en cas de travaux afin de garantir la possibilité des interventions des entreprises.
Echafaudages
La mise en place de nacelles pour les travaux sur les immeubles de plus de 8 étages à faciliter les travaux de percements en façade pour le chauffagiste et un gain de temps important, de plus avec moins d’efforts pour le transport des matériels et outillages.
Problématique échafaudages
A l’inverse les nacelles ont été prises à partie dans le cadre de la mise en place des couvertines toitures, il y a plusieurs réunions entre entreprises et MOA/MOE, qui ont abouties tardivement à une solution validée par tous.
5S
Une information a été communiquée vers toutes les entreprises. L’entreprise de façade a vraiment pris en compte cet objectif, les alentours du chantier sont très convenables et les stocks sont parfaitement lisibles.
Les autres entreprises n’ont pas cette problématique et alimentent le chantier car elles sont en flux tendu.
LPS
Les plannings ont souvent été mal renseignés sans beaucoup de visibilité (à 1 semaine seulement), toutes les entreprises ont joué le jeu pour alimenter le LPS et être présentes pour la réunion hebdomadaire.
Contrôle des travaux
Un aspect que toutes les entreprises ont renseigné, très visuel et répondant en grande partie à une vision des travaux de chacun.
La MOA a effectué une visite de chantier hebdomadaire pour valider les avancements et régler les points bloquants, notamment avec les locataires.
Avancement des travaux
Les engagements pris par les entreprises ont été en grande partie respectés.
Les indicateurs de performance ont permis de contrôler les points bloquants du chantier et y remédier en temps réel.
Cette expérience Lean Construction sur le chantier d’Epinal a également été menée en partenariat avec la CARAST Nord-Est et l’INRS que nous remercions.
Action expérimentale en Nouvelle Aquitaine
Action expérimentale 2017-2018
Démarche d’optimisation de la production et de réduction des gaspillages sur chantier lean construction.
Télécharger le rapport complet
Démarche d’optimisation de la production et de réduction des gaspillages sur chantier
LEAN CONSTRUCTION
Cet ouvrage est le fruit d’une étude menée sur un chantier expérimental par la FFB Nouvelle Aquitaine, avec l’aide de l’OPPBTP et quatre stagiaires issus d’écoles d’ingénieurs de Charente Maritime. Maîtrise d’ouvrage et maîtrise d’œuvre se sont prêtées à l’expérimentation, ce qui nous a permis d’approfondir les résultats encourageants constatés lors du premier chantier.
Des ressources
Note méthodologique
Lean Construction tous métiers
Site Internet Delta-Partners
Partenaire de Villavenir
Batimétiers
Lean Construction des chantiers plus performants